Introduction
The purpose of this blog is to leverage SAP’s Digital manufacturing and SAP-MII capabilities to Integrate diversified manufacturing processes, machines, and systems together to bring smart manufactring concepts (Industry 4.0 ) into reality. 80% of the data is generated on the shop floor, If we would able to capture all those data using a comprehensive integration framework and contextualize with business acumen, then this would potentially solve all manufacturing related issues and help archiving.
◉ High yield.
◉ Low no-confirmities.
◉ High OEE(overall equipment effectiveness).
◉ Predict potential disruption and downstream impacts.
Every company and manufacturing processes and system are different in nature in terms of technology as well as maturity. This blog will help and provide practical approach to Integrate processes, shopfloor systems, and machines together as per their maturity levels.
What is Industry 4.0 and Evolution of Manufacturing Industry Automation?
Industrial 1.0
The First Industrial Revolution began in the 18th century through the use of steam power and mechanization of production. What before produced threads on simple spinning wheels, the mechanized version achieved eight times the volume at the same time. Steam power was already known. The use of it for industrial purposes was the greatest breakthrough for increasing human productivity. Instead of weaving looms powered by muscle, steam engines could be used for power. Developments such as the steamship or (some 100 years later) the steam-powered locomotive brought about further massive changes because humans and goods could move great distances in fewer hours.
Industrial 2.0
The Second Industrial Revolution began in the 19th century through the discovery of electricity and assembly line production. Henry Ford (1863-1947) took the idea of mass production from a slaughterhouse in Chicago: The pigs hung from conveyor belts and each butcher performed only a part of the task of butchering the animal. Henry Ford carried over these principles into automobile production and drastically altered them in the process. While before one station assembled an entire automobile, now the vehicles were produced in partial steps on the conveyor belt – significantly faster and at a lower cost.
3rd Industry 3.0
The Third Industrial Revolution began in the ’70s in the 20th century through partial automation using memory-programmable controls and computers. Since the introduction of these technologies, we are now able to automate an entire production process – without human assistance. Known examples of this are robots that perform programmed sequences without human intervention.
Industry 4.0
We are currently implementing the Fourth Industrial Revolution. This is characterized by the application of information and communication technologies to the manufacturing engineering process industry and is also known as “Industry 4.0”. It builds on the developments of the Third Industrial Revolution. Production systems that already have computer technology are expanded by a network connection and have a digital twin on the Internet so to speak. These allow communication with other facilities and the output of information about themselves. This is the next step in production automation. The networking of all systems leads to “cyber-physical production systems” and therefore smart factories, in which production systems, components and people communicate via a network and production is nearly autonomous.
What are the Need for Manufacturing Intelligence and Integration and use of SAP-MII?
The industry has a dearth need of expert tools/solutions based on Data science and computer algorithms to FastTrack corrective medicine production & market launch as well as preventive vaccines development. SAP Manufacturing Integration and Intelligence (SAP -MII) is an SAP application for synchronizing manufacturing operations with both back-office business processes and standardized data. This is the enabler of the implementation of centralized procedural controls in distributed manufacturing and execution facilities.
It functions as a data hub between central SAP ERP and satellite systems of operational applications. Moreover, SAP MII can be leveraged to contextualize the data to prescribe appropriate intelligent responses to Shopfloor machines/applications.
SAP Manufacturing Integration and Intelligence (SAP MII) connects your plant operations and enterprise systems, so employees, materials, processes, and machines work seamlessly together. The on-premise solution enables access to the data and analytics needed to make critical business decisions. This greater visibility into your operations supports improving productivity and overall equipment effectiveness.
What is the business needs to be addressed?
1. Ability to see all progress of Shop orders
2. Ability to report actual time of consumption of component materials
3. Ability to see nonconformities and open CAPA
4. Ability to see batches on hold with reason code
5. Ability to see downstream Impact on batches on hold
6. Ability to enter/view data related to Imperfection Tracking
7. Ability to see environment exposure and remaining environmental life
8. Ability to create end to end electronic batch records
9. Ability to Integrate with all satellite execution systems/applications such as
◉ PLC based machines / SCADA
◉ Environment tracking system
◉ Laboratory Information System (LIMS)
◉ Compliance System TrackWise
Refer Figure1- To see integrated shop floor monitoring and control needs
Figure 1: Central ERP system Connected with satellite systems Via SAP MII
What is the implementation framework?
Every product that reaches an end customer represents the cumulative effort of the entire manufacturing ecosystem. Unless all the systems are integrated seamlessly and overall efficiency and total quality will be ensured.
Please refer to Figure 2 to understand the implementation framework. Here glossary of the abbreviation is used.
1. PP – Production Planning
2. QM – Quality Management
3. PP-PI – Production planning for the process industry
4. MM – Material Management
5. RFC – Remote Function Call (Secure electronic interaction between systems)
6. MD – Master Data ( Data on which transactions are being performed)
7. BM – Batch Management (material that is intended to have uniform. character and quality, within specified limits, and is produced in a single cycle)
8. GR – Goods Receipt (Received finished/Semi Finished goods after manufacturing)
9. GI – Goods Issue (Issue component for Manufacturing)
10. KPI – Key performance index.
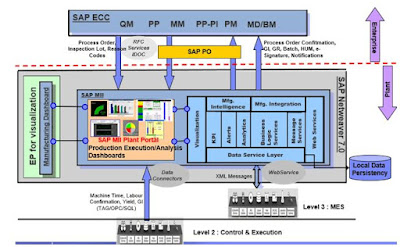
Figure 2 – Schematic Architecture Diagram
What is Application Level Architecture?
Please refer Figure – 2 to 6 for detailed technical architecture.
1. SAP ECC will send the control recipes to SAP MII when the order is released.
2. SAP MII receiving the messages from SAP ECC will buffer them in the system database and subsequently run a pre-defined rule to process the messages to create the work center task-list. ECC System or S/4 HANA must be the source of truth for master data.
3. Operators can log in to the SAP MII portal and view the resource schedule in the Production Dashboard. This can happen in offline mode to SAP ECC, as the data are already available in SAP MII.
4. The operator can create order confirmations, quality inspections, and other relevant tasks from the dashboard which will be updated in SAP ECC. SAP MII can provide guaranteed delivery for asynchronous messages.
5. The dashboard will also provide real-time information about machine status, early warnings for machine failures or quality issues and shall provide the user with possible options.
6. Production Supervisor and Shift Supervisors can have a real-time view of the production process and monitor and analyze different KPIs such as OEE.
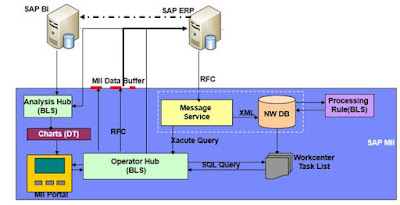
Figure 3: Application Architecture
Refer Figure-4: SAP ECC Sends Manufacturing Order Information to Execution system Via SAP -MII
◉ Use control recipe (process order) to send the order data from ECC to MII.
◉ If the control recipe is considered what will be the PI categories used.
Figure 4 : Get Data Function
Refer Figure 5 & 6: To understand how does SAP MII Buffers Message and Create Work center Task List and provides order schedule, Quality Inspection schedule to shop floor supervisor.
◉ If quality Phases are in place in the master recipe in Case 03 inspection type (We have to capture QA11 transaction in Dashboard).
◉ Resource task list will display the list of control recipes along with order number, material, start, and end date, status
Figure 5:Production Operators Views Workcenter and Task List
Figure 6: Bi-directional Information Exchange
Refer Figure 7: To understand one stop shop for Production Operators to Performs Order Execution. This interface make the operator Operators equipped with all the information, he needs to perform his/her job.
◉ What are the information displayed in the Production Dashboard (e.g. Phase list, material list) ?
◉ What are the operations performed from the production dashboard (e.g. order confirmation – TT or TE; QM inspection; batch creation, etc)?
◉ What are the plant systems integrated to retrieve relevant data (e.g. Historian, LIMS, etc)?
◉ Phase confirmation (time-event)
◉ Confirmation cancellation (Transaction code: CORS should be considered from dashboard).
◉ GI (Inventory manage).
◉ Batch Derivative for Expiry date calculation.
◉ Quality check as per quality plan (Inspection lot)
◉ GR (digital signature) with batch creation (?): Batch Creation Should be at or before order release.
◉ PM notification (phase confirmation – yield)
◉ Material Rejection (final or material/component)
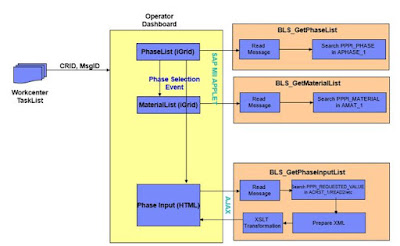
Figure 7: Operational Dashboard services
Business Case study
This business case study is all about integrating shop floor systems involved in manufacturing of lifesaving medical diagnostic slides using SAP -MII and SAP Digital Manufacturing Suite.
One of world’s largest medical diagnostic manufacturers serving the transfusion medicine community and laboratories around the world. The client is the leading provider of diagnostic slides for screening, diagnosing chemicals, monitoring, confirming diseases early with presence across the world in laboratories.
Clients wants to build to real-time production execution system along with integration of all shop floor systems including ODS, Machine SQL databases and environment tracking system called Spider, Laboratory testing System (LIMS) and compliance system (TrackWise) with centralized SAP ECC using SAP-MII.
successful Implementation of Manufacturing Automation for a Major Medical Devices & Diagnostics Client using SAP – MII and Integration of Complex Processes and Various Systems on a single portal based platform.
What was the Business Problem Statement?
Manufacturing and Testing running on multiple standalone systems (MDM, SAP R/2, TRACK wise, LIMS, PALE, SPIDER etc):
◉ These were not well integrated with each other.
◉ Manual interventions in the process resulted in human error and subsequently caused product non-conformance.
◉ Outdated systems with scalability, product support, and compliance issues.
◉ High losses and long elapsed time due to standalone system and application.
◉ High nonconformities and low regulatory confidence
Manufacturing starts with a complex Formulation process for preparing solutions to be used in different diagnostics requirements and for dry slide technology.
◉ Formulation Process – for Coating Solution manufacturing
◉ Coating Process – for coating the Solution on film rolls
◉ Imperfection Tracking Process – for recording non-conformity imperfection tracking across the entire roll
◉ Slitting Process – to cut coated rolls into slits
◉ Slide Assembly Process – to cut slits into slides
◉ Packaging Process – packing of slides
◉ Manufacturing of Analyzer Equipment.
The client wanted an integrated design with a smart solution having minimal human interference as part of their SAP implementation program.
What was the proposed Solution Approach?
MII (Manufacturing Integration and Intelligence) was used to integrate SAP and Legacy systems.
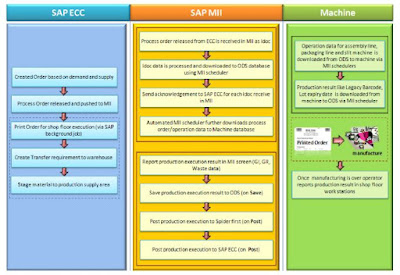
Figure 8: Process step
1. Shop floor processes for Slide Manufacturing run on Process Orders created in ECC based on production planning, demand from customer sales orders, and available material stock.
2. Download released process order from ECC and stage to ODS staging database.
3. Download relevant process order and operational data to automated work center database.
4. Report process order execution result(Goods Issue, Goods Receipt, Waste) through MII.
5. Calculate and validate critical business data accurately based on the reported result.
6. Post-process order confirmation to SAP ECC via Spider and display real-time response.
Figure 9: Illustration of custom formulation screen
Figure 10:Illustration of Imperfection Tracking
A complex custom logic functionality tracks the Imperfections recorded across Batch and assists Manufacturing to remove Imperfections downstream by providing a geometrical (lengthwise/widthwise) view of Imperfections. This functionality is necessary in order to meet the FDA/ISO which mandates that non-conforming material is removed and/or flagged for removal from the product before it is released to the next manufacturing process.
Figure 11: Imperfection Tracking Screen
What are the value propositions?
1. Integrated disconnected shop-floor systems with SAP and Non-SAP systems across the plant.
2. Got rid of complex old R2 based ECC transactions for entering production execution results.
3. Avoid erroneous manual calculation of manufacturing data causing delay and financial impacts.
Improved operator efficiency by providing easy-to-use reporting screens and shortening data reporting time.
4. Timely plan and organize manufacturing operations to satisfy customer demand.
5. Track down and report real-time product expiration information in the system and avoid paper-based tracking
Source: sap.com
No comments:
Post a Comment